
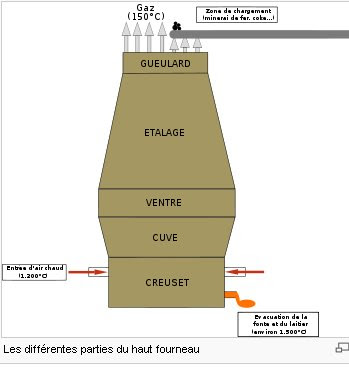
Les premiers haut-fourneaux sont apparus en Chine vers l'an mil av. J.-C. ; utilisés pour la poterie, ils permettaient déjà d'atteindre la température de fusion du fer, mais ils n'ont pas été utilisés tout de suite en métallurgie. Les chinois inventeront la fonte durant la période des Royaumes combattants (IVe siècle av. J.-C.– 220 av. J.-C.).
Au cours du XIVe siècle, la force hydraulique est appliquée pour la ventilation des foyers ou bas fourneaux utilisés pour extraire le fer du minerai. L'utilisation de roues à aubes ou à godets en remplacement de la force humaine permet d'augmenter la puissance des vents. Ceci permit l'augmentation de la hauteur des fours jusqu'à atteindre quatre à cinq mètres. Avec un fourneau de cette hauteur et les températures permises par les nouveaux soufflets, le fer une fois réduit se combinait au carbone, produisant de la fonte, dont la température de fusion (environ 1200°) est nettement inférieure à celle du fer pur. On obtenait donc de la fonte liquide au bas du fourneau, et non plus la loupe de fer pâteux qu'il fallait jusque là extraire du fourneau pour l'amener à forger.
Le lieu et la date précise d'apparition des hauts fourneaux ne sont pas encore établis avec certitude ; ils semblent avoir été connus au XIVe siècle dans la région de Liège ; des structures fouillées en Suède et datée du XIIIe siècle pourraient également être des fourneaux de ce type. Ils se généralisent au XVe siècle dans la plus grande partie de l'Europe du Nord.
La conséquence majeure de la production de fonte est que les hauts fourneaux peuvent fonctionner en continu, la fonte étant périodiquement coulée, alors que le bas fourneau doit être arrêté pour extraire la loupe qui s'y est formée. Au XVIIIe siècle, la durée d'allumage des hauts fourneaux allait généralement de cinq à neuf mois en fonction de la disponibilité de l'énergie hydraulique ; ils étaient rechargés par le gueulard en charbon de bois, minerai et castine (un additif calcaire permettant une meilleure évacuation des impuretés sous la forme d'un laitier) ; la fonte était coulée une à deux fois par jour.
En 1709 a lieu la première coulée au coke au Royaume-Uni à Coalbrookdale (Shropshire) par Abraham Darby (1678–1717). Le coke remplace le charbon de bois dans l'alimentation du fourneau ; il est produit par désoufrage de la houille. Le procédé au coke est perfectionné par le fils et petit-fils de Abraham Darby (qui s'appellent également Abraham Darby). Cependant, la fonte produite de cette manière est dans un premier temps impropre à l'affinage (décarburation pour produire du fer forgé), ce qui explique qu'à cette époque l'utilisation du coke ne se généralise pas. En 1760, le Royaume-Uni ne compte que dix-sept hauts fourneaux au coke et ce n'est qu'en 1780 que son usage se généralise.
En France, les premiers essais au coke n'ont lieu qu'en 1769 à Hayange (aujourd'hui dans le département français de la Moselle) avant que soient construits, sous la direction du Britannique William Wilkinson, les hauts fourneaux au coke du Creusot. Cette production peine cependant à concurrencer la production traditionnelle au charbon de bois : elle ne la dépasse qu'en 1853, à la faveur de l'explosion de la demande due au développement du chemin de fer. En 1860, encore un tiers de la fonte française est produite dans des hauts fourneaux au charbon de bois.
Au XIXe siècle l'utilisation du coke provoque un changement radical dans la technique. La hauteur des hauts fourneaux atteint trente mètres. Les soufflets sont remplacés par des pistons en fonte actionnés par la vapeur.
En 1828, le Britannique Neilson à l'idée de chauffer les vents (air injectés dans le bas du haut fourneau). En 1829, il réalise la première machine industrielle qui chauffe l'air à 150°C (à Clyde, au Royaume-Uni). Ceci permet d'économiser un tiers du charbon par rapport au procédé de l'époque. Le procédé est rapidement adopté. En 1870, les Britanniques Cooper et Whitwell mettent au point un procédé utilisant les gaz chauds et combustibles rejetés par le haut fourneau pour chauffer les vents.
Du point de vue du lexique, on peut dire que l'histoire du mot devance en quelque sorte l'histoire de l'objet. On rencontre en effet haut fourneau dès le XVe siècle. Mais jusqu'au XIXe siècle, cette appellation côtoie régulièrement d'autres appellations comme fourneau, fourneau à fer, fourneau de fusion, grand fourneau, fourneau élevé, etc. Ces noms renvoient tous à un fourneau de coulée par opposition au bas fourneau à loupe. Mais les hauteurs, qui varient de 5 à 20 mètres, ne jouent aucun rôle. Dans les relevés nombre de fourneaux sont plus hauts que des hauts fourneaux. Ce n'est qu'au milieu du XIXe siècle, que l'objet rejoint le nom. Comme l'écrit Roland Eluerd : "Poli par quatre siècles d'histoire, le nom haut fourneau pouvait devenir le pur symbole de la modernité, superbe présent du passé au vocabulaire d'une sidérurgie où le fourneau, dressé à plus de quarante mètres, véritable signal de l'entreprise, deviendrait incontestablement le haut fourneau." (Les Mots du fer et des Lumières, Paris, Champion, 1993, p. 192).
Capacités et production
À titre indicatif, en 1806, la production de fonte dans un haut fourneau est de 4 tonnes/jour, en 1850 elle passe à 15 tonnes/jour. En 1974, le haut fourneau 4 d'Arcelor Dunkerque, avec ses 14 m de diamètre au creuset (ce diamètre est la donnée la plus significative pour juger la capacité) s'adjuge le record européen. Il peut fournir plus de 10 000 tonnes de fonte par jour.
Cependant, aujourd'hui, la plupart des hauts fourneaux, ont une taille légèrement plus petite, même si chaque rénovation d'un creuset est généralement une opportunité pour augmenter sa taille. Un diamètre de 11 m pour une production journalière de 6 400 t/jour est caractéristique d'un gros haut fourneau moderne. Ce tonnage correspond bien aux capacités des outils situés en aval, à l'aciérie.
Parallèlement à l'augmentation de la taille, l'abandon des minerais pauvres, comme la minette lorraine, a permis, à dimension égale, de quasiment doubler la production d'un haut fourneau.
Parmi les coproduits issus d'un haut fourneau, on peut citer :
le laitier de haut fourneau, valorisé dans les travaux publics. Pour un haut fourneau fonctionnant avec des minerais de fer riches, on atteint généralement une proportion 317 kg de laitierde manière régulière pour 1 tonne de fonte produite.
le gaz récupéré au gueulard, qui correspond à l'air chaud injecté au creuset, dont l'oxygène est devenu du monoxyde de carbone, est un bon combustible.
Il faut aussi mentionner le haut fourneau comme un outil de production du manganèse. Actuellement, 30 % de la production de manganèse est issu de cette filière (le reste étant élaboré au four électrique).
Au cours du XIVe siècle, la force hydraulique est appliquée pour la ventilation des foyers ou bas fourneaux utilisés pour extraire le fer du minerai. L'utilisation de roues à aubes ou à godets en remplacement de la force humaine permet d'augmenter la puissance des vents. Ceci permit l'augmentation de la hauteur des fours jusqu'à atteindre quatre à cinq mètres. Avec un fourneau de cette hauteur et les températures permises par les nouveaux soufflets, le fer une fois réduit se combinait au carbone, produisant de la fonte, dont la température de fusion (environ 1200°) est nettement inférieure à celle du fer pur. On obtenait donc de la fonte liquide au bas du fourneau, et non plus la loupe de fer pâteux qu'il fallait jusque là extraire du fourneau pour l'amener à forger.
Le lieu et la date précise d'apparition des hauts fourneaux ne sont pas encore établis avec certitude ; ils semblent avoir été connus au XIVe siècle dans la région de Liège ; des structures fouillées en Suède et datée du XIIIe siècle pourraient également être des fourneaux de ce type. Ils se généralisent au XVe siècle dans la plus grande partie de l'Europe du Nord.
La conséquence majeure de la production de fonte est que les hauts fourneaux peuvent fonctionner en continu, la fonte étant périodiquement coulée, alors que le bas fourneau doit être arrêté pour extraire la loupe qui s'y est formée. Au XVIIIe siècle, la durée d'allumage des hauts fourneaux allait généralement de cinq à neuf mois en fonction de la disponibilité de l'énergie hydraulique ; ils étaient rechargés par le gueulard en charbon de bois, minerai et castine (un additif calcaire permettant une meilleure évacuation des impuretés sous la forme d'un laitier) ; la fonte était coulée une à deux fois par jour.
En 1709 a lieu la première coulée au coke au Royaume-Uni à Coalbrookdale (Shropshire) par Abraham Darby (1678–1717). Le coke remplace le charbon de bois dans l'alimentation du fourneau ; il est produit par désoufrage de la houille. Le procédé au coke est perfectionné par le fils et petit-fils de Abraham Darby (qui s'appellent également Abraham Darby). Cependant, la fonte produite de cette manière est dans un premier temps impropre à l'affinage (décarburation pour produire du fer forgé), ce qui explique qu'à cette époque l'utilisation du coke ne se généralise pas. En 1760, le Royaume-Uni ne compte que dix-sept hauts fourneaux au coke et ce n'est qu'en 1780 que son usage se généralise.
En France, les premiers essais au coke n'ont lieu qu'en 1769 à Hayange (aujourd'hui dans le département français de la Moselle) avant que soient construits, sous la direction du Britannique William Wilkinson, les hauts fourneaux au coke du Creusot. Cette production peine cependant à concurrencer la production traditionnelle au charbon de bois : elle ne la dépasse qu'en 1853, à la faveur de l'explosion de la demande due au développement du chemin de fer. En 1860, encore un tiers de la fonte française est produite dans des hauts fourneaux au charbon de bois.
Au XIXe siècle l'utilisation du coke provoque un changement radical dans la technique. La hauteur des hauts fourneaux atteint trente mètres. Les soufflets sont remplacés par des pistons en fonte actionnés par la vapeur.
En 1828, le Britannique Neilson à l'idée de chauffer les vents (air injectés dans le bas du haut fourneau). En 1829, il réalise la première machine industrielle qui chauffe l'air à 150°C (à Clyde, au Royaume-Uni). Ceci permet d'économiser un tiers du charbon par rapport au procédé de l'époque. Le procédé est rapidement adopté. En 1870, les Britanniques Cooper et Whitwell mettent au point un procédé utilisant les gaz chauds et combustibles rejetés par le haut fourneau pour chauffer les vents.
Du point de vue du lexique, on peut dire que l'histoire du mot devance en quelque sorte l'histoire de l'objet. On rencontre en effet haut fourneau dès le XVe siècle. Mais jusqu'au XIXe siècle, cette appellation côtoie régulièrement d'autres appellations comme fourneau, fourneau à fer, fourneau de fusion, grand fourneau, fourneau élevé, etc. Ces noms renvoient tous à un fourneau de coulée par opposition au bas fourneau à loupe. Mais les hauteurs, qui varient de 5 à 20 mètres, ne jouent aucun rôle. Dans les relevés nombre de fourneaux sont plus hauts que des hauts fourneaux. Ce n'est qu'au milieu du XIXe siècle, que l'objet rejoint le nom. Comme l'écrit Roland Eluerd : "Poli par quatre siècles d'histoire, le nom haut fourneau pouvait devenir le pur symbole de la modernité, superbe présent du passé au vocabulaire d'une sidérurgie où le fourneau, dressé à plus de quarante mètres, véritable signal de l'entreprise, deviendrait incontestablement le haut fourneau." (Les Mots du fer et des Lumières, Paris, Champion, 1993, p. 192).
Capacités et production
À titre indicatif, en 1806, la production de fonte dans un haut fourneau est de 4 tonnes/jour, en 1850 elle passe à 15 tonnes/jour. En 1974, le haut fourneau 4 d'Arcelor Dunkerque, avec ses 14 m de diamètre au creuset (ce diamètre est la donnée la plus significative pour juger la capacité) s'adjuge le record européen. Il peut fournir plus de 10 000 tonnes de fonte par jour.
Cependant, aujourd'hui, la plupart des hauts fourneaux, ont une taille légèrement plus petite, même si chaque rénovation d'un creuset est généralement une opportunité pour augmenter sa taille. Un diamètre de 11 m pour une production journalière de 6 400 t/jour est caractéristique d'un gros haut fourneau moderne. Ce tonnage correspond bien aux capacités des outils situés en aval, à l'aciérie.
Parallèlement à l'augmentation de la taille, l'abandon des minerais pauvres, comme la minette lorraine, a permis, à dimension égale, de quasiment doubler la production d'un haut fourneau.
Parmi les coproduits issus d'un haut fourneau, on peut citer :
le laitier de haut fourneau, valorisé dans les travaux publics. Pour un haut fourneau fonctionnant avec des minerais de fer riches, on atteint généralement une proportion 317 kg de laitierde manière régulière pour 1 tonne de fonte produite.
le gaz récupéré au gueulard, qui correspond à l'air chaud injecté au creuset, dont l'oxygène est devenu du monoxyde de carbone, est un bon combustible.
Il faut aussi mentionner le haut fourneau comme un outil de production du manganèse. Actuellement, 30 % de la production de manganèse est issu de cette filière (le reste étant élaboré au four électrique).
Constitution et fonctionnement
Les différentes parties du haut fourneau
La cuve, de forme cylindrique élargie dans le 1/4 de sa base, est constituée de briques réfractaires soutenues par une armature extérieure de poutrelles métalliques.
Le chargement s'effectue par le haut (minerai de fer, déchets ferreux, coke ou « Charbon »).
La récupération de la fonte s'opère par coulée au bas du four.
Une injection d'air est effectuée au plus large du four, afin d'entretenir la combustion du charbon, permettant ainsi la fusion de tous les éléments.
A l'opposé du point de coulée de la fonte on opère une coulée de laitier, récupération des déchets de la fusion, ou scories.
La température est variable en fonction de la hauteur dans la cuve (de haut en bas):
300 °C au niveau du gueulard, phase de dessiccation;
400 °C à 800 °C, phase de réduction;
900 °C à 1 200 °C, phase de carburation;
1 800 °C, phase de fusion;
1 600 °C, phase de liquéfaction, lieu des coulées.
Compte tenu de la forte présence de carbone au cours du processus, le produit obtenu est un alliage fer-carbone de type fonte (taux de carbone supérieur à 2.1 %).
Les différentes parties du haut fourneau
La cuve, de forme cylindrique élargie dans le 1/4 de sa base, est constituée de briques réfractaires soutenues par une armature extérieure de poutrelles métalliques.
Le chargement s'effectue par le haut (minerai de fer, déchets ferreux, coke ou « Charbon »).
La récupération de la fonte s'opère par coulée au bas du four.
Une injection d'air est effectuée au plus large du four, afin d'entretenir la combustion du charbon, permettant ainsi la fusion de tous les éléments.
A l'opposé du point de coulée de la fonte on opère une coulée de laitier, récupération des déchets de la fusion, ou scories.
La température est variable en fonction de la hauteur dans la cuve (de haut en bas):
300 °C au niveau du gueulard, phase de dessiccation;
400 °C à 800 °C, phase de réduction;
900 °C à 1 200 °C, phase de carburation;
1 800 °C, phase de fusion;
1 600 °C, phase de liquéfaction, lieu des coulées.
Compte tenu de la forte présence de carbone au cours du processus, le produit obtenu est un alliage fer-carbone de type fonte (taux de carbone supérieur à 2.1 %).
Les réactions chimiques
Le haut fourneau est un réacteur chimique, dont le fonctionnement à contre-courant (les gaz montent alors que la matière solide descend) lui assure un excellent rendement thermique.
Aucun commentaire:
Enregistrer un commentaire