mercredi 14 janvier 2009
mercredi 7 janvier 2009
office de la formation professionnelle et du la promotion du travail

Pour préparer les entreprises aux formations et métiers de demain, l’Office de la formation professionnelle et de la promotion du travail (OFPPT) en collaboration avec la Chambre française de commerce et d’industrie au Maroc (CFCIM) a organisé, le 18 avril à Casablanca, une rencontre dédiée au plan Emergence.
L’OFPPT a déjà investi dans la formation de quelque 400.000 jeunes à l’horizon 2007-2008 et également mobilisé ses moyens pour s’attaquer aux secteurs stratégiques pour le développement national.
1er opérateur de formation professionnelle, l’Ofppt dispense des formations dans 170 métiers dans différents secteurs, dont l’offshoring qui représente une opportunité pour le Maroc. Avec la vague de développement des centres d’appels, une étude a été réalisée pour prévoir les besoins de cette activité en plein essor économique. C’est ainsi que l’Office accompagne ce plan avec un projet étalé sur 3 ans et visant la formation de 6.900 lauréats. Des partenaires étrangers comme Cnam, Cisco et Oracle travaillent avec l’OFPPT pour offrir des formations ciblées correspondant aux attentes des entreprises. « Ce qui est rassurant, c’est que les entreprises sont preneuses avant même la fin du cursus », confie Saïd Slaoui, directeur de recherche et ingénierie de formation.
L’OFPPT a déjà investi dans la formation de quelque 400.000 jeunes à l’horizon 2007-2008 et également mobilisé ses moyens pour s’attaquer aux secteurs stratégiques pour le développement national.
1er opérateur de formation professionnelle, l’Ofppt dispense des formations dans 170 métiers dans différents secteurs, dont l’offshoring qui représente une opportunité pour le Maroc. Avec la vague de développement des centres d’appels, une étude a été réalisée pour prévoir les besoins de cette activité en plein essor économique. C’est ainsi que l’Office accompagne ce plan avec un projet étalé sur 3 ans et visant la formation de 6.900 lauréats. Des partenaires étrangers comme Cnam, Cisco et Oracle travaillent avec l’OFPPT pour offrir des formations ciblées correspondant aux attentes des entreprises. « Ce qui est rassurant, c’est que les entreprises sont preneuses avant même la fin du cursus », confie Saïd Slaoui, directeur de recherche et ingénierie de formation.
la construction metallique

La première moitié du XIXe siècle est marquée en Europe par la Révolution industrielle, dans laquelle l'essor de la métallurgie joue un rôle essentiel.
La fonte fait son entrée en 1779 dans le champ de la construction avec le pont de Coalbrookdale en Angleterre, et en France avec le pont des Arts en 1803. Les structures métalliques commencent à se répandre dans les usines textiles, les charpentes des théâtres ou les serres. Le fer laminé s'impose vers 1845 comme un matériau plus efficace et plus économique que la fonte, ouvrant la voie à un spectaculaire renouvellement des formes construites. Les Halles de Paris édifiées en 1853 par Victor Baltard et Félix Callet sont en France le premier édifice important où le métal est ouvertement montré. Elles ouvrent la voie à de nouvelles typologies d'édifices exigés par la société industrielle, tels que gares, marchés, usines, grands magasins, verrières, kiosques, pavillons d'exposition. L'architecture du fer s'épanouit alors, pour constituer l'une des créations les plus originales et les plus spectaculaires du XIXesiècle, grâce à ses qualités d'élégance aérienne, de légèreté, de transparence, mêlées de force brute, de puissance contenue, de tension extrême.
Vers 1885, à l'époque de la construction de la Tour, l'usage du fer et de l'acier s'est largement répandu dans les ponts et les charpentes.
Les ingénieurs affirment leur rôle croissant dans l'architecture à travers la maîtrise du calcul et de la construction. Le pont sur le Firth of Forth en Écosse, inauguré en 1889, atteint des portées record de 521 mètres. On envisage même de franchir la Manche avec un pont aux portées encore plus grandes. Aux États-Unis, on commence à employer l'acier pour ériger à Chicago des immeubles de grande hauteur.
La Construction Métallique, une filière professionnelle originale et passionnante !
Un projet de construction métallique pour aboutir se doit d'associer à une intense vie d'équipe, la maîtrise de techniques très variées. Pour cette raison la construction métallique est l'un des secteurs les plus enviés des jeunes et des moins jeunes qui ont le goût de l'aventure. C'est aussi un secteur du BTP en plein développement.
Un grand choix de Formation pour travailler dans la Construction Métallique !
Nos formations vous feront entrer dans cet univers professionnel. Vous serez peu à peu familiarisés avec les nombreuses techniques d'assemblage, de montage et de logistiques qui font la spécificité de la profession. Vous entrerez progressivement dans la vie de ce secteur du BTP par les stages que vous y ferez et pour lesquels nous vous accompagnerons dans vos recherches.
Les formations de l'Ecole Chez Soi s'adressent à tous les publics
Quel que soit votre niveau d'étude, l'Ecole Chez Soi a LA FORMATION qui convient à votre projet professionnel ! Vous étudiez le dessin, les techniques de construction, les techniques d'assemblage et les matériaux, vous vous initiez progressivement aux calculs... et vous réalisez des projets concrets tirés de cas réels. Les débouchés sont nombreux et le secteur ne parvient pas à recruter autant qu'il le souhaite. Nos étudiants sont en plus très recherchés des entreprises. En effet, l'Ecole Chez Soi est partenaire du syndicat national de la construction métallique !
Désignation des métaux et alliages

Alliage d'aluminium destinés au corroyage
Il s'agit des alliages destinées à être transformés par déformation (laminage, forgeage, filage etc).
Désignation numérique
Il s'agit des alliages destinées à être transformés par déformation (laminage, forgeage, filage etc).
Désignation numérique
Les alliages d'aluminium pour corroyage sont référencés par une désignation de 4 chiffres. Cette désignation est conforme aux directives de l'Aluminum Association (Washington DC 20006, USA), ce qui donne par exemple : 7075. Les quatre chiffres sont parfois précédés par les lettres AA (exemple : AA 6061), acronyme de « Aluminum Association ». Les quatre chiffres sont parfois suivis par une lettre qui indique une variante nationale d'une composition existante.
Cette désignation a été reprise en Europe par la norme EN 573-3 en ajoutant les préfixe EN, A (aluminium) et W (wrought : mot anglais signifiant corroyage). Ce qui donne EN AW-7075. Dans les faits, très souvent, seuls les quatre chiffres sont utilisés.
Cette notation à quatre chiffres est très usitée internationalement et a dans la pratique remplacé les anciennes appellations nationales.
Le premier chiffre indique l'élément d'addition principal de l'alliage :
1XXX (série des 1000) : alliage comportant au minimum 99% d'aluminium (exemple : 1050)
2XXX (série des 2000) : cuivre (exemple 2024)
3XXX (série des 3000) : Manganèse (exemple : 3003)
4XXX (série des 4000) : silicium (exemple : 4006)
5XXX (série des 5000) : magnésium (exemple : 5083)
6XXX (série des 6000) : magnésium, silicium (exemple : 6061)
7XXX (série des 7000) : zinc (exemple : 7020)
8XXX (série des 8000) : autres éléments.
Le deuxième chiffre indique une variante (exemple : 7075 comporte 0,50 % de fer et le 7175 plus pur comporte 0,20% de fer). Les troisième et quatrième chiffres sont des numéros d'ordre et servent à identifier l'alliage.La seule exception est la série 1000, ces deux derniers chiffres y indiquant le pourcentage d'aluminium (exemple : 1050 qui comporte au minimum 99,50% d'aluminium).
Désignation ISO
Il s'agit d'une désignation utilisant les symboles chimiques dite souvent ISO (suivant ISO 209-1 : aluminium et alliages d'aluminium corroyés - Composition chimique et formes des produits. Partie 1 : composition chimique).
Elle est très peu usitée.
Exemple : Al Cu4 Mg Si
Désignation alphanumérique européenne
Cette désignation a été reprise en Europe par la norme EN 573-3 en ajoutant les préfixe EN, A (aluminium) et W (wrought : mot anglais signifiant corroyage). Ce qui donne EN AW-7075. Dans les faits, très souvent, seuls les quatre chiffres sont utilisés.
Cette notation à quatre chiffres est très usitée internationalement et a dans la pratique remplacé les anciennes appellations nationales.
Le premier chiffre indique l'élément d'addition principal de l'alliage :
1XXX (série des 1000) : alliage comportant au minimum 99% d'aluminium (exemple : 1050)
2XXX (série des 2000) : cuivre (exemple 2024)
3XXX (série des 3000) : Manganèse (exemple : 3003)
4XXX (série des 4000) : silicium (exemple : 4006)
5XXX (série des 5000) : magnésium (exemple : 5083)
6XXX (série des 6000) : magnésium, silicium (exemple : 6061)
7XXX (série des 7000) : zinc (exemple : 7020)
8XXX (série des 8000) : autres éléments.
Le deuxième chiffre indique une variante (exemple : 7075 comporte 0,50 % de fer et le 7175 plus pur comporte 0,20% de fer). Les troisième et quatrième chiffres sont des numéros d'ordre et servent à identifier l'alliage.La seule exception est la série 1000, ces deux derniers chiffres y indiquant le pourcentage d'aluminium (exemple : 1050 qui comporte au minimum 99,50% d'aluminium).
Désignation ISO
Il s'agit d'une désignation utilisant les symboles chimiques dite souvent ISO (suivant ISO 209-1 : aluminium et alliages d'aluminium corroyés - Composition chimique et formes des produits. Partie 1 : composition chimique).
Elle est très peu usitée.
Exemple : Al Cu4 Mg Si
Désignation alphanumérique européenne
Il existe une norme européenne qui décrit des appellations très proches des appellations de type ISO. Cette norme porte la référence EN 573-2 (Aluminium et alliages d'aluminium - Composition chimique et forme des produits corroyés - Partie 2 : système de désignation fondé sur les symboles chimiques). En principe, cette appellation ne doit pas être utilisée seule mais doit être mise derrière l'appellation numérique, entre crochets.
Elle est très peu usitée.
Exemples : EN AW-2024 [Al Cu4Mg1], EN AW-6060 [Al Mg Si], EN AW-7075 [Al Zn5,5MgCu] (désignation exacte suivant la série de norme EN 573)
Ancienne désignation française
Cette désignation était décrite dans la norme NF A 02-004 (annulée). Elle s'appuyait sur une codification des éléments chimiques différente de la nomenclature habituelle chimique (aluminium : A, cuivre : U, zinc : Z etc). Elle donnait également une indication sur les pourcentages d'éléments contenu dans l'alliage.
Cette appellation n'est plus utilisée pour les alliages de corroyage.
Aluminium
Exemple : A7
Alliages d'aluminium
Exemple : A-U4G, A-G4MC, A-GS, A-Z5GU
Tableau d'équivalence entre différentes appellations
Elle est très peu usitée.
Exemples : EN AW-2024 [Al Cu4Mg1], EN AW-6060 [Al Mg Si], EN AW-7075 [Al Zn5,5MgCu] (désignation exacte suivant la série de norme EN 573)
Ancienne désignation française
Cette désignation était décrite dans la norme NF A 02-004 (annulée). Elle s'appuyait sur une codification des éléments chimiques différente de la nomenclature habituelle chimique (aluminium : A, cuivre : U, zinc : Z etc). Elle donnait également une indication sur les pourcentages d'éléments contenu dans l'alliage.
Cette appellation n'est plus utilisée pour les alliages de corroyage.
Aluminium
Exemple : A7
Alliages d'aluminium
Exemple : A-U4G, A-G4MC, A-GS, A-Z5GU
Tableau d'équivalence entre différentes appellations
Avertissement : ce tableau est donné à titre purement indicatif, il existe parfois des différences entre les compositions malgré l'équivalence. Certaines appellations étant anciennes, il peut y avoir eu des évolutions depuis la disparition de certaines d'entres elles.
Rappel : l'appellation à 4 chiffres (éventuellement précédée du préfixe AA) type Aluminum Association est à privilégier. C'est aujourd'hui l'appellation la plus utilisée.
Rappel : l'appellation à 4 chiffres (éventuellement précédée du préfixe AA) type Aluminum Association est à privilégier. C'est aujourd'hui l'appellation la plus utilisée.
Normes et documents
EN 573-1 : Aluminium et alliages d'aluminium - Composition chimique et forme des produits corroyés - Partie 1 : système de désignation numérique.
EN 573-2 : Aluminium et alliages d'aluminium - Composition chimique et forme des produits corroyés - Partie 2 : système de désignation fondé sur les symboles chimiques.
EN 573-3 : Aluminium et alliages d'aluminium - Composition chimique et forme des produits corroyés - Partie 3 : composition chimique .
EN 573-4 : Aluminium et alliages d'aluminium - Composition chimique et forme des produits corroyés - Partie 4 : formes des produits
PR EN 573-5 (projet) : Aluminium et alliages d'aluminium - Composition chimique et forme des produits corroyés - Partie 5 : codification des produits corroyés normalisés
ISO 209-1 : Aluminium et alliages d'aluminium corroyés - Composition chimique et formes des produits. Partie 1 : composition chimique
Aluminum Association : Internationl Alloy Designations and Chemical Composition Limits for Wrought Aluminum and Wrought Aluminum Association. (téléchargeable sur le site de l'Aluminum Association :
Alliage d'aluminium destinés à la fonderie
EN 573-1 : Aluminium et alliages d'aluminium - Composition chimique et forme des produits corroyés - Partie 1 : système de désignation numérique.
EN 573-2 : Aluminium et alliages d'aluminium - Composition chimique et forme des produits corroyés - Partie 2 : système de désignation fondé sur les symboles chimiques.
EN 573-3 : Aluminium et alliages d'aluminium - Composition chimique et forme des produits corroyés - Partie 3 : composition chimique .
EN 573-4 : Aluminium et alliages d'aluminium - Composition chimique et forme des produits corroyés - Partie 4 : formes des produits
PR EN 573-5 (projet) : Aluminium et alliages d'aluminium - Composition chimique et forme des produits corroyés - Partie 5 : codification des produits corroyés normalisés
ISO 209-1 : Aluminium et alliages d'aluminium corroyés - Composition chimique et formes des produits. Partie 1 : composition chimique
Aluminum Association : Internationl Alloy Designations and Chemical Composition Limits for Wrought Aluminum and Wrought Aluminum Association. (téléchargeable sur le site de l'Aluminum Association :
Alliage d'aluminium destinés à la fonderie
Il s'agit des alliages destinées à être transformés par moulage (fonderie d'aluminium).
Désignation numérique
Désignation numérique
Les alliages d'aluminium pour fonderie sont référencés par une désignation de 5 chiffres.
Cette désignation a été reprise en Europe par la norme EN 1780-1 en ajoutant les préfixe EN, A (aluminium) et C (casting : mot anglais signifiant fonderie). Ce qui donne EN AC-43100 par exemple. Dans les faits, très souvent, seuls les cinq chiffres sont utilisés.
Cette notation à cinq chiffres est usitée internationalement mais la france reste plutôt attachée à une ancienne désignation décrite plus bas.
Le premier chiffre indique l'élément d'addition principal de l'alliage :
(série des 20000) : cuivre (exemple 21000)
(série des 40000) : silicium (exemple : 43300)
(série des 50000) : magnésium (exemple : 51200)
(série des 70000) : zinc (exemple : 71000)
Le deuxième chiffre indique le groupe de l'alliage. Cette notion de groupe est utilisée pour les alliages normalisés (EN 1706). Chaque groupe présente un ensemble de caractéristiques mécaniques et/ou physiques similaires. Par exemple les alliages du groupe AlSi ont une composition proche de l'eutectique aluminium-silicium (12,6 % en masse) ce qui leur confére une excellente aptitude à la coulée.
Les trois chiffres suivant indiquent une variante (exemple : 43100 comporte 0,10 % de cuivre et le 43200 plus pur comporte 0,35% de cuivre, les proportions de zinc et nickel, de plomb et de titane varient aussi entre ces deux alliages, dans des proportions similaires). Les trois chiffres suivant sont des numéros d'ordre et servent à identifier l'alliage.
Désignation chimique
Il s'agit d'une désignation utilisant les symboles chimiques (suivant EN 1780-2 : Aluminium et alliages d'aluminium - Système de désignation applicable aux lingots pour refusion en aluminium allié, aux alliages-mères et aux produits moulés - Partie 2 : système de désignation basé sur les symboles chimiques.).
Elle est très peu usitée.
Exemple : Al Cu4 Mg Ti pour le 21000
Cette désignation a été reprise en Europe par la norme EN 1780-1 en ajoutant les préfixe EN, A (aluminium) et C (casting : mot anglais signifiant fonderie). Ce qui donne EN AC-43100 par exemple. Dans les faits, très souvent, seuls les cinq chiffres sont utilisés.
Cette notation à cinq chiffres est usitée internationalement mais la france reste plutôt attachée à une ancienne désignation décrite plus bas.
Le premier chiffre indique l'élément d'addition principal de l'alliage :
(série des 20000) : cuivre (exemple 21000)
(série des 40000) : silicium (exemple : 43300)
(série des 50000) : magnésium (exemple : 51200)
(série des 70000) : zinc (exemple : 71000)
Le deuxième chiffre indique le groupe de l'alliage. Cette notion de groupe est utilisée pour les alliages normalisés (EN 1706). Chaque groupe présente un ensemble de caractéristiques mécaniques et/ou physiques similaires. Par exemple les alliages du groupe AlSi ont une composition proche de l'eutectique aluminium-silicium (12,6 % en masse) ce qui leur confére une excellente aptitude à la coulée.
Les trois chiffres suivant indiquent une variante (exemple : 43100 comporte 0,10 % de cuivre et le 43200 plus pur comporte 0,35% de cuivre, les proportions de zinc et nickel, de plomb et de titane varient aussi entre ces deux alliages, dans des proportions similaires). Les trois chiffres suivant sont des numéros d'ordre et servent à identifier l'alliage.
Désignation chimique
Il s'agit d'une désignation utilisant les symboles chimiques (suivant EN 1780-2 : Aluminium et alliages d'aluminium - Système de désignation applicable aux lingots pour refusion en aluminium allié, aux alliages-mères et aux produits moulés - Partie 2 : système de désignation basé sur les symboles chimiques.).
Elle est très peu usitée.
Exemple : Al Cu4 Mg Ti pour le 21000
Normes et documents
EN 1780-1 : Aluminium et alliages d'aluminium - Système de désignation applicable aux lingots pour refusion en aluminium allié, aux alliages-mères et aux produits moulés - Partie 1 : système de désignation numérique.
EN 1780-2 : Aluminium et alliages d'aluminium - Système de désignation applicable aux lingots pour refusion en aluminium allié, aux alliages-mères et aux produits moulés - Partie 2 : système de désignation basé sur les symboles chimiques.
EN 1780-3 : Aluminium et alliages d'aluminium - Système de désignation applicable aux lingots pour refusion en aluminium allié, aux alliages-mères et aux produits moulés - Partie 3 : règles d'écriture pour la composition chimique.
EN 12258-1 : Aluminium et alliages d'aluminium - termes et définitions.
Pour la fonderie, le bureau de normalisation français est B.N.I.F.
Voir aussi
EN 1780-1 : Aluminium et alliages d'aluminium - Système de désignation applicable aux lingots pour refusion en aluminium allié, aux alliages-mères et aux produits moulés - Partie 1 : système de désignation numérique.
EN 1780-2 : Aluminium et alliages d'aluminium - Système de désignation applicable aux lingots pour refusion en aluminium allié, aux alliages-mères et aux produits moulés - Partie 2 : système de désignation basé sur les symboles chimiques.
EN 1780-3 : Aluminium et alliages d'aluminium - Système de désignation applicable aux lingots pour refusion en aluminium allié, aux alliages-mères et aux produits moulés - Partie 3 : règles d'écriture pour la composition chimique.
EN 12258-1 : Aluminium et alliages d'aluminium - termes et définitions.
Pour la fonderie, le bureau de normalisation français est B.N.I.F.
Voir aussi
Alliages d'aluminium pour corroyage
Alliages d'aluminium pour fonderie
Cuivre et alliages de cuivre
Cuivres
Exemple : Cu-ETP
Alliages de cuivre
Exemple : Cu Zn39 Pb2
Fer et alliages ferreux
Alliages d'aluminium pour fonderie
Cuivre et alliages de cuivre
Cuivres
Exemple : Cu-ETP
Alliages de cuivre
Exemple : Cu Zn39 Pb2
Fer et alliages ferreux
fonte
Fontes à graphite lamellaire (non alliées)
par exemple: EN-GJL-350
-> EN : European Norm (Norme Européenne)
-> GJL: Fonte à graphite lamellaire
-> 350: Résistance minimale à la rupture par traction (Rr en MPa)
Fontes à graphite sphéroïdal (non alliées)
par exemple: EN-GJS-450-10
-> EN : European Norm (Norme Européenne)
-> GJS: Fonte à graphite sphéroïdal
-> 450: Résistance minimale à la rupture par traction (Rr en MPa)
-> 10 : Allongement après rupture en %
Fontes malléables (non alliées)
par exemple: EN-GJMB-550-4
-> EN : European Norm (Norme Européenne)
-> GJMB : Fonte malléable à cœur noir (Black)
-> 550: Résistance minimale à la rupture par traction (Rr en MPa)
-> 4: Allongement après rupture en %
autre exemple: EN-GJMW-380-12
-> EN : European Norm (Norme Européenne)
-> GJMW : Fonte malléable à cœur blanc (White)
-> 380: Résistance minimale à la rupture par traction (Rr en MPa)
-> 12: Allongement après rupture en %
Fontes austénitiques (alliées)
par exemple: EN-GJS Ni Cr 30-1
-> EN : European Norm (Norme Européenne)
-> GJS: Fonte à graphite sphéroïdal alliée
-> Ni: Nickel avec 30%
-> Cr: Chrome avec 1%
par exemple: EN-GJN Cr15Mo Ni
-> EN : European Norm (Norme Européenne)
-> GJN: Fonte blanche alliée
-> Cr: Chrome avec 15%
-> Mo: Molybdène avec quelques traces
-> Ni: Nickel avec quelques traces
Aciers
Aciers d'usage général
Aciers spéciaux (non alliés) pour traitement thermique
Aciers faiblements alliés
Aciers fortement alliés
Aciers de constructions
Zinc et alliages de zinc
Exemple : Z - A4G, cependant, on utilise fréquemment la désignation « ZL » pour Zinc-Aluminium suivie de la teneur (arrondie) en aluminium de l'alliage.
Il est utilisé pour le revêtement, en tôle, ou pour la galvanisation (on recouvre de zinc), et sous forme d’alliage. Ils sont toujours moulés.
D'une manière générale, les alliages de zinc normalisés en fonderie sont des alliages zinc-aluminium avec des teneurs variables en aluminium (de 4 à 30%), de faibles additions de magnésium (de 0.012 à 0.06%) et de cuivre (de 0 à 3%).
Les alliages ZL3, ZL5 et ZL2 (zamak) sont essentiellement utilisés en moulage sous pression (pour les pignons et les fermetures éclairs par exemple), ils représentent environ 95% du marché.Leur composition est définie par les normes NF EN 1774 « Zinc et alliages de zinc - Alliages pour fonderie - Lingots et liquide » et NF 12844 "Zinc et Alliages de zinc - Pièces moulées - Spécifications", ainsi que la norme internationale ISO 301.
Les alliages Kayem utilisés pour la fabrication économique d'outillages de presse (outils de découpe et d'emboutissage, moules d’injection, de thermoformage des matières plastiques).
Les alliages ZL8, ZL12 et ZL27 (ZA) avec:
Le ZL8 qui apporte une bonne tenue en température, présente un ensemble de propriétés mécaniques d'un très bon niveau et qui est moulable sur les machines à chambre chaude,
Le ZL12 (ILZRO 12) principalement utilisé dans la réalisation de prototypes ou de pré-séries de pièces qui seront ensuite réalisées en Zamak par moulage sous pression,
Le ZL27 qui se caractérise par une charge de rupture élevée (de 400 à 450 MPa). C'est le seul alliage susceptible de recevoir un traitement thermique d'homogénéisation qui améliore sa ductilité. Il existe également d'autres alliages spéciaux qui répondent à des exigences particulières de résistance au frottement ou de tenue en température.
les hauts fourneaux

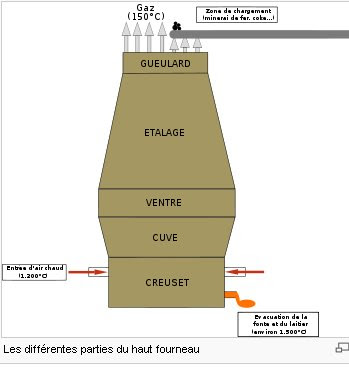
Les premiers haut-fourneaux sont apparus en Chine vers l'an mil av. J.-C. ; utilisés pour la poterie, ils permettaient déjà d'atteindre la température de fusion du fer, mais ils n'ont pas été utilisés tout de suite en métallurgie. Les chinois inventeront la fonte durant la période des Royaumes combattants (IVe siècle av. J.-C.– 220 av. J.-C.).
Au cours du XIVe siècle, la force hydraulique est appliquée pour la ventilation des foyers ou bas fourneaux utilisés pour extraire le fer du minerai. L'utilisation de roues à aubes ou à godets en remplacement de la force humaine permet d'augmenter la puissance des vents. Ceci permit l'augmentation de la hauteur des fours jusqu'à atteindre quatre à cinq mètres. Avec un fourneau de cette hauteur et les températures permises par les nouveaux soufflets, le fer une fois réduit se combinait au carbone, produisant de la fonte, dont la température de fusion (environ 1200°) est nettement inférieure à celle du fer pur. On obtenait donc de la fonte liquide au bas du fourneau, et non plus la loupe de fer pâteux qu'il fallait jusque là extraire du fourneau pour l'amener à forger.
Le lieu et la date précise d'apparition des hauts fourneaux ne sont pas encore établis avec certitude ; ils semblent avoir été connus au XIVe siècle dans la région de Liège ; des structures fouillées en Suède et datée du XIIIe siècle pourraient également être des fourneaux de ce type. Ils se généralisent au XVe siècle dans la plus grande partie de l'Europe du Nord.
La conséquence majeure de la production de fonte est que les hauts fourneaux peuvent fonctionner en continu, la fonte étant périodiquement coulée, alors que le bas fourneau doit être arrêté pour extraire la loupe qui s'y est formée. Au XVIIIe siècle, la durée d'allumage des hauts fourneaux allait généralement de cinq à neuf mois en fonction de la disponibilité de l'énergie hydraulique ; ils étaient rechargés par le gueulard en charbon de bois, minerai et castine (un additif calcaire permettant une meilleure évacuation des impuretés sous la forme d'un laitier) ; la fonte était coulée une à deux fois par jour.
En 1709 a lieu la première coulée au coke au Royaume-Uni à Coalbrookdale (Shropshire) par Abraham Darby (1678–1717). Le coke remplace le charbon de bois dans l'alimentation du fourneau ; il est produit par désoufrage de la houille. Le procédé au coke est perfectionné par le fils et petit-fils de Abraham Darby (qui s'appellent également Abraham Darby). Cependant, la fonte produite de cette manière est dans un premier temps impropre à l'affinage (décarburation pour produire du fer forgé), ce qui explique qu'à cette époque l'utilisation du coke ne se généralise pas. En 1760, le Royaume-Uni ne compte que dix-sept hauts fourneaux au coke et ce n'est qu'en 1780 que son usage se généralise.
En France, les premiers essais au coke n'ont lieu qu'en 1769 à Hayange (aujourd'hui dans le département français de la Moselle) avant que soient construits, sous la direction du Britannique William Wilkinson, les hauts fourneaux au coke du Creusot. Cette production peine cependant à concurrencer la production traditionnelle au charbon de bois : elle ne la dépasse qu'en 1853, à la faveur de l'explosion de la demande due au développement du chemin de fer. En 1860, encore un tiers de la fonte française est produite dans des hauts fourneaux au charbon de bois.
Au XIXe siècle l'utilisation du coke provoque un changement radical dans la technique. La hauteur des hauts fourneaux atteint trente mètres. Les soufflets sont remplacés par des pistons en fonte actionnés par la vapeur.
En 1828, le Britannique Neilson à l'idée de chauffer les vents (air injectés dans le bas du haut fourneau). En 1829, il réalise la première machine industrielle qui chauffe l'air à 150°C (à Clyde, au Royaume-Uni). Ceci permet d'économiser un tiers du charbon par rapport au procédé de l'époque. Le procédé est rapidement adopté. En 1870, les Britanniques Cooper et Whitwell mettent au point un procédé utilisant les gaz chauds et combustibles rejetés par le haut fourneau pour chauffer les vents.
Du point de vue du lexique, on peut dire que l'histoire du mot devance en quelque sorte l'histoire de l'objet. On rencontre en effet haut fourneau dès le XVe siècle. Mais jusqu'au XIXe siècle, cette appellation côtoie régulièrement d'autres appellations comme fourneau, fourneau à fer, fourneau de fusion, grand fourneau, fourneau élevé, etc. Ces noms renvoient tous à un fourneau de coulée par opposition au bas fourneau à loupe. Mais les hauteurs, qui varient de 5 à 20 mètres, ne jouent aucun rôle. Dans les relevés nombre de fourneaux sont plus hauts que des hauts fourneaux. Ce n'est qu'au milieu du XIXe siècle, que l'objet rejoint le nom. Comme l'écrit Roland Eluerd : "Poli par quatre siècles d'histoire, le nom haut fourneau pouvait devenir le pur symbole de la modernité, superbe présent du passé au vocabulaire d'une sidérurgie où le fourneau, dressé à plus de quarante mètres, véritable signal de l'entreprise, deviendrait incontestablement le haut fourneau." (Les Mots du fer et des Lumières, Paris, Champion, 1993, p. 192).
Capacités et production
À titre indicatif, en 1806, la production de fonte dans un haut fourneau est de 4 tonnes/jour, en 1850 elle passe à 15 tonnes/jour. En 1974, le haut fourneau 4 d'Arcelor Dunkerque, avec ses 14 m de diamètre au creuset (ce diamètre est la donnée la plus significative pour juger la capacité) s'adjuge le record européen. Il peut fournir plus de 10 000 tonnes de fonte par jour.
Cependant, aujourd'hui, la plupart des hauts fourneaux, ont une taille légèrement plus petite, même si chaque rénovation d'un creuset est généralement une opportunité pour augmenter sa taille. Un diamètre de 11 m pour une production journalière de 6 400 t/jour est caractéristique d'un gros haut fourneau moderne. Ce tonnage correspond bien aux capacités des outils situés en aval, à l'aciérie.
Parallèlement à l'augmentation de la taille, l'abandon des minerais pauvres, comme la minette lorraine, a permis, à dimension égale, de quasiment doubler la production d'un haut fourneau.
Parmi les coproduits issus d'un haut fourneau, on peut citer :
le laitier de haut fourneau, valorisé dans les travaux publics. Pour un haut fourneau fonctionnant avec des minerais de fer riches, on atteint généralement une proportion 317 kg de laitierde manière régulière pour 1 tonne de fonte produite.
le gaz récupéré au gueulard, qui correspond à l'air chaud injecté au creuset, dont l'oxygène est devenu du monoxyde de carbone, est un bon combustible.
Il faut aussi mentionner le haut fourneau comme un outil de production du manganèse. Actuellement, 30 % de la production de manganèse est issu de cette filière (le reste étant élaboré au four électrique).
Au cours du XIVe siècle, la force hydraulique est appliquée pour la ventilation des foyers ou bas fourneaux utilisés pour extraire le fer du minerai. L'utilisation de roues à aubes ou à godets en remplacement de la force humaine permet d'augmenter la puissance des vents. Ceci permit l'augmentation de la hauteur des fours jusqu'à atteindre quatre à cinq mètres. Avec un fourneau de cette hauteur et les températures permises par les nouveaux soufflets, le fer une fois réduit se combinait au carbone, produisant de la fonte, dont la température de fusion (environ 1200°) est nettement inférieure à celle du fer pur. On obtenait donc de la fonte liquide au bas du fourneau, et non plus la loupe de fer pâteux qu'il fallait jusque là extraire du fourneau pour l'amener à forger.
Le lieu et la date précise d'apparition des hauts fourneaux ne sont pas encore établis avec certitude ; ils semblent avoir été connus au XIVe siècle dans la région de Liège ; des structures fouillées en Suède et datée du XIIIe siècle pourraient également être des fourneaux de ce type. Ils se généralisent au XVe siècle dans la plus grande partie de l'Europe du Nord.
La conséquence majeure de la production de fonte est que les hauts fourneaux peuvent fonctionner en continu, la fonte étant périodiquement coulée, alors que le bas fourneau doit être arrêté pour extraire la loupe qui s'y est formée. Au XVIIIe siècle, la durée d'allumage des hauts fourneaux allait généralement de cinq à neuf mois en fonction de la disponibilité de l'énergie hydraulique ; ils étaient rechargés par le gueulard en charbon de bois, minerai et castine (un additif calcaire permettant une meilleure évacuation des impuretés sous la forme d'un laitier) ; la fonte était coulée une à deux fois par jour.
En 1709 a lieu la première coulée au coke au Royaume-Uni à Coalbrookdale (Shropshire) par Abraham Darby (1678–1717). Le coke remplace le charbon de bois dans l'alimentation du fourneau ; il est produit par désoufrage de la houille. Le procédé au coke est perfectionné par le fils et petit-fils de Abraham Darby (qui s'appellent également Abraham Darby). Cependant, la fonte produite de cette manière est dans un premier temps impropre à l'affinage (décarburation pour produire du fer forgé), ce qui explique qu'à cette époque l'utilisation du coke ne se généralise pas. En 1760, le Royaume-Uni ne compte que dix-sept hauts fourneaux au coke et ce n'est qu'en 1780 que son usage se généralise.
En France, les premiers essais au coke n'ont lieu qu'en 1769 à Hayange (aujourd'hui dans le département français de la Moselle) avant que soient construits, sous la direction du Britannique William Wilkinson, les hauts fourneaux au coke du Creusot. Cette production peine cependant à concurrencer la production traditionnelle au charbon de bois : elle ne la dépasse qu'en 1853, à la faveur de l'explosion de la demande due au développement du chemin de fer. En 1860, encore un tiers de la fonte française est produite dans des hauts fourneaux au charbon de bois.
Au XIXe siècle l'utilisation du coke provoque un changement radical dans la technique. La hauteur des hauts fourneaux atteint trente mètres. Les soufflets sont remplacés par des pistons en fonte actionnés par la vapeur.
En 1828, le Britannique Neilson à l'idée de chauffer les vents (air injectés dans le bas du haut fourneau). En 1829, il réalise la première machine industrielle qui chauffe l'air à 150°C (à Clyde, au Royaume-Uni). Ceci permet d'économiser un tiers du charbon par rapport au procédé de l'époque. Le procédé est rapidement adopté. En 1870, les Britanniques Cooper et Whitwell mettent au point un procédé utilisant les gaz chauds et combustibles rejetés par le haut fourneau pour chauffer les vents.
Du point de vue du lexique, on peut dire que l'histoire du mot devance en quelque sorte l'histoire de l'objet. On rencontre en effet haut fourneau dès le XVe siècle. Mais jusqu'au XIXe siècle, cette appellation côtoie régulièrement d'autres appellations comme fourneau, fourneau à fer, fourneau de fusion, grand fourneau, fourneau élevé, etc. Ces noms renvoient tous à un fourneau de coulée par opposition au bas fourneau à loupe. Mais les hauteurs, qui varient de 5 à 20 mètres, ne jouent aucun rôle. Dans les relevés nombre de fourneaux sont plus hauts que des hauts fourneaux. Ce n'est qu'au milieu du XIXe siècle, que l'objet rejoint le nom. Comme l'écrit Roland Eluerd : "Poli par quatre siècles d'histoire, le nom haut fourneau pouvait devenir le pur symbole de la modernité, superbe présent du passé au vocabulaire d'une sidérurgie où le fourneau, dressé à plus de quarante mètres, véritable signal de l'entreprise, deviendrait incontestablement le haut fourneau." (Les Mots du fer et des Lumières, Paris, Champion, 1993, p. 192).
Capacités et production
À titre indicatif, en 1806, la production de fonte dans un haut fourneau est de 4 tonnes/jour, en 1850 elle passe à 15 tonnes/jour. En 1974, le haut fourneau 4 d'Arcelor Dunkerque, avec ses 14 m de diamètre au creuset (ce diamètre est la donnée la plus significative pour juger la capacité) s'adjuge le record européen. Il peut fournir plus de 10 000 tonnes de fonte par jour.
Cependant, aujourd'hui, la plupart des hauts fourneaux, ont une taille légèrement plus petite, même si chaque rénovation d'un creuset est généralement une opportunité pour augmenter sa taille. Un diamètre de 11 m pour une production journalière de 6 400 t/jour est caractéristique d'un gros haut fourneau moderne. Ce tonnage correspond bien aux capacités des outils situés en aval, à l'aciérie.
Parallèlement à l'augmentation de la taille, l'abandon des minerais pauvres, comme la minette lorraine, a permis, à dimension égale, de quasiment doubler la production d'un haut fourneau.
Parmi les coproduits issus d'un haut fourneau, on peut citer :
le laitier de haut fourneau, valorisé dans les travaux publics. Pour un haut fourneau fonctionnant avec des minerais de fer riches, on atteint généralement une proportion 317 kg de laitierde manière régulière pour 1 tonne de fonte produite.
le gaz récupéré au gueulard, qui correspond à l'air chaud injecté au creuset, dont l'oxygène est devenu du monoxyde de carbone, est un bon combustible.
Il faut aussi mentionner le haut fourneau comme un outil de production du manganèse. Actuellement, 30 % de la production de manganèse est issu de cette filière (le reste étant élaboré au four électrique).
Constitution et fonctionnement
Les différentes parties du haut fourneau
La cuve, de forme cylindrique élargie dans le 1/4 de sa base, est constituée de briques réfractaires soutenues par une armature extérieure de poutrelles métalliques.
Le chargement s'effectue par le haut (minerai de fer, déchets ferreux, coke ou « Charbon »).
La récupération de la fonte s'opère par coulée au bas du four.
Une injection d'air est effectuée au plus large du four, afin d'entretenir la combustion du charbon, permettant ainsi la fusion de tous les éléments.
A l'opposé du point de coulée de la fonte on opère une coulée de laitier, récupération des déchets de la fusion, ou scories.
La température est variable en fonction de la hauteur dans la cuve (de haut en bas):
300 °C au niveau du gueulard, phase de dessiccation;
400 °C à 800 °C, phase de réduction;
900 °C à 1 200 °C, phase de carburation;
1 800 °C, phase de fusion;
1 600 °C, phase de liquéfaction, lieu des coulées.
Compte tenu de la forte présence de carbone au cours du processus, le produit obtenu est un alliage fer-carbone de type fonte (taux de carbone supérieur à 2.1 %).
Les différentes parties du haut fourneau
La cuve, de forme cylindrique élargie dans le 1/4 de sa base, est constituée de briques réfractaires soutenues par une armature extérieure de poutrelles métalliques.
Le chargement s'effectue par le haut (minerai de fer, déchets ferreux, coke ou « Charbon »).
La récupération de la fonte s'opère par coulée au bas du four.
Une injection d'air est effectuée au plus large du four, afin d'entretenir la combustion du charbon, permettant ainsi la fusion de tous les éléments.
A l'opposé du point de coulée de la fonte on opère une coulée de laitier, récupération des déchets de la fusion, ou scories.
La température est variable en fonction de la hauteur dans la cuve (de haut en bas):
300 °C au niveau du gueulard, phase de dessiccation;
400 °C à 800 °C, phase de réduction;
900 °C à 1 200 °C, phase de carburation;
1 800 °C, phase de fusion;
1 600 °C, phase de liquéfaction, lieu des coulées.
Compte tenu de la forte présence de carbone au cours du processus, le produit obtenu est un alliage fer-carbone de type fonte (taux de carbone supérieur à 2.1 %).
Les réactions chimiques
Le haut fourneau est un réacteur chimique, dont le fonctionnement à contre-courant (les gaz montent alors que la matière solide descend) lui assure un excellent rendement thermique.
la resistance des materiaux

La résistance des matériaux, notée RDM, est une branche simplifiée de la mécanique des milieux continus permettant le calcul des contraintes et déformations dans les structures (machines, génie mécanique, bâtiments, génie civil).
Cette science permet de ramener la loi de comportement globale d'une structure (relation entre sollicitations — forces ou couple — et déplacements) à une loi de comportement locale des matériaux (relation entre contraintes et déformations). L'objectif étant de dimensionner la structure suivant des critères de résistance, de déplacement admissible (souvent improprement appelé déformation) et de coût financier.
Lorsque l'intensité de la contrainte augmente, il y a d'abord déformation élastique (le matériau reprend sa forme initiale lorsque la sollicitation disparaît), puis déformation plastique (le matériaux ne reprend pas sa forme initiale lorsque la sollicitation disparaît, il subsiste une déformation résiduelle), et enfin rupture (la sollicitation dépasse la résistance intrinsèque du matériau).
Sommaire
Cette science permet de ramener la loi de comportement globale d'une structure (relation entre sollicitations — forces ou couple — et déplacements) à une loi de comportement locale des matériaux (relation entre contraintes et déformations). L'objectif étant de dimensionner la structure suivant des critères de résistance, de déplacement admissible (souvent improprement appelé déformation) et de coût financier.
Lorsque l'intensité de la contrainte augmente, il y a d'abord déformation élastique (le matériau reprend sa forme initiale lorsque la sollicitation disparaît), puis déformation plastique (le matériaux ne reprend pas sa forme initiale lorsque la sollicitation disparaît, il subsiste une déformation résiduelle), et enfin rupture (la sollicitation dépasse la résistance intrinsèque du matériau).
Sommaire
Hypothèses de la RDM
En première approximation le modèle RDM est valide dans un domaine limité par les hypothèses suivantes :
Le matériau est :
élastique (pas de plastification, le matériau reprend sa forme initiale après un cycle chargement déchargement),
linéaire (pas de non-linéarité, les contraintes sont proportionnelles aux déformations),
homogène (pas de variation de comportement dans le matériau),
isotrope (le comportement est le même quel que soit la direction).
Le problème est :
iso-statique (pièce en équilibre cinématique),
En petits déplacements (pas de grand déplacement),
quasi-statique (pas d'effet dynamique),
quasi-isotherme (pas de changement de température
En première approximation le modèle RDM est valide dans un domaine limité par les hypothèses suivantes :
Le matériau est :
élastique (pas de plastification, le matériau reprend sa forme initiale après un cycle chargement déchargement),
linéaire (pas de non-linéarité, les contraintes sont proportionnelles aux déformations),
homogène (pas de variation de comportement dans le matériau),
isotrope (le comportement est le même quel que soit la direction).
Le problème est :
iso-statique (pièce en équilibre cinématique),
En petits déplacements (pas de grand déplacement),
quasi-statique (pas d'effet dynamique),
quasi-isotherme (pas de changement de température
Base de résolution
Le Principe de Saint-Venant stipule qu'une condition limite (au point M) peut être remplacée par un chargement équivalent sans modifier notablement le problème , si l'on se place suffisamment "loin" de M.
Remplacement des conditions limites par un chargement,
Notion d'erreur à "proximité" des conditions limites.
Le Principe de Navier-Bernoulli précise que les sections droites à la fibre moyenne (pour les poutres) ou au plan moyen (pour les plaques et coques) restent planes après déformation.
La Loi de Hooke précise que, dans le domaine de l'élasticité de la matière, les déformations sont proportionnelles aux contraintes.
Le Principe de superposition permet de décomposer toute sollicitation complexe en somme de sollicitations simples. Ce principe est directement lié à l'hypothèse de linéarité de la loi de Hooke.
L'équilibre statique donne la base de la résolution du problème. Il stipule que :
La somme des forces extérieures au système est égale au vecteur nul :
Le Principe de Saint-Venant stipule qu'une condition limite (au point M) peut être remplacée par un chargement équivalent sans modifier notablement le problème , si l'on se place suffisamment "loin" de M.
Remplacement des conditions limites par un chargement,
Notion d'erreur à "proximité" des conditions limites.
Le Principe de Navier-Bernoulli précise que les sections droites à la fibre moyenne (pour les poutres) ou au plan moyen (pour les plaques et coques) restent planes après déformation.
La Loi de Hooke précise que, dans le domaine de l'élasticité de la matière, les déformations sont proportionnelles aux contraintes.
Le Principe de superposition permet de décomposer toute sollicitation complexe en somme de sollicitations simples. Ce principe est directement lié à l'hypothèse de linéarité de la loi de Hooke.
L'équilibre statique donne la base de la résolution du problème. Il stipule que :
La somme des forces extérieures au système est égale au vecteur nul :
Inscription à :
Articles (Atom)